Introduction:
Pneumatic cylinders, often referred to as air cylinders, are essential components in the world of industrial automation. These devices convert compressed air into mechanical motion, providing precise and controlled linear or rotary movement. This article delves into the working principles, types, applications, and advantages of pneumatic cylinders in various industries.
Working Principles:
Pneumatic cylinders operate on the principles of fluid dynamics and the mechanical properties of gases. Compressed air, acting as the working fluid, is introduced into the cylinder. This air pressure creates a force that moves a piston or a rod inside the cylinder. The movement of the piston is then transferred to the attached mechanism, resulting in the desired action, such as lifting, pushing, pulling, or rotating.
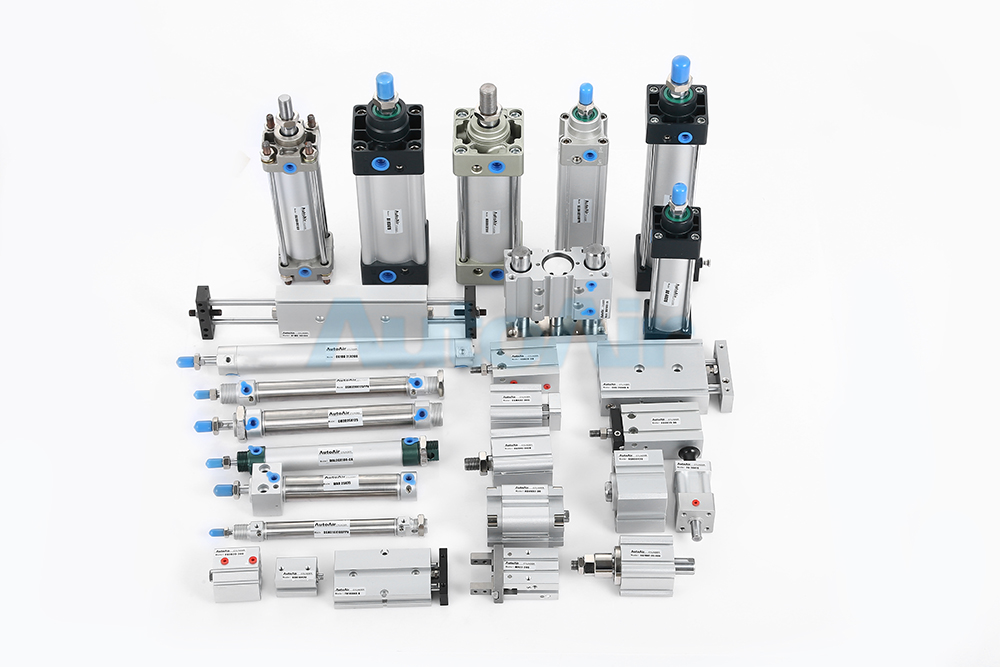
Types of Pneumatic Cylinders:
Single-Acting Cylinders: These cylinders exert force in only one direction, typically using spring force or external loads to return the piston to its initial position.
Double-Acting Cylinders: These cylinders can apply force in both directions. Compressed air is alternately applied to either side of the piston, allowing bidirectional movement.
Rotary Cylinders: Instead of linear motion, these cylinders produce rotary motion. They are used to achieve rotational movements in automation systems.
Rodless Cylinders: These cylinders feature a piston that moves within a tubular housing, eliminating the need for an extending rod. They are used where space is limited.
Applications:
Pneumatic cylinders find applications in a wide range of industries due to their efficiency, simplicity, and cost-effectiveness. In manufacturing, they power robotic arms, conveyor systems, and material handling equipment. Automotive assembly lines utilize pneumatic cylinders for processes like welding, painting, and component positioning. In the packaging industry, they control filling, sealing, and labeling processes. Pneumatic cylinders also play a role in medical equipment, aerospace systems, and even amusement park rides.
Advantages of Pneumatic Cylinders:
Speed and Precision: Pneumatic cylinders provide fast response times and precise control over motion, making them suitable for applications that require rapid and accurate movements.
Safety: Compressed air is a safe and clean power source that eliminates the risk of electrical hazards, making pneumatic systems suitable for hazardous environments.
Cost-Effective: Pneumatic systems are often more economical to install and maintain compared to hydraulic or electric systems.
Reliability: Pneumatic cylinders are robust and can endure harsh conditions without performance degradation, contributing to system reliability.
Challenges and Innovations:
Despite their advantages, pneumatic cylinders can face challenges such as air leakage, inconsistent motion, and inefficiencies. Engineers continually develop innovative solutions, including improved seal designs, advanced control systems, and energy-efficient components. Smart pneumatic systems equipped with sensors and automation technologies further enhance the performance and predictive maintenance capabilities of pneumatic cylinders.
Conclusion:
Pneumatic cylinders serve as the workhorses of industrial automation, driving efficient and precise mechanical motion across various industries. Their adaptability, reliability, and ease of use make them indispensable for a wide array of applications. As technology evolves, pneumatic cylinders are expected to continue evolving, enabling further advancements in automation, manufacturing, and beyond.
Post time: Aug-30-2023